Industrial ventilation and dust/fume collection are critical for manufacturers to ensure worker safety, product quality, and regulatory compliance.
Let’s delve into the critical needs:
1. Regulatory Compliance
-
- Manufacturers must meet standards set by OSHA, NFPA, and EPA regarding air quality, hazardous emissions, and combustible dust safety. Failure to comply with regulations can lead to fines, shutdowns, or legal liabilities.
- Industrial ventilation systems help manufacturers comply with environmental regulations by controlling the release of pollutants, particulate matter, and chemical fumes into the atmosphere.
2. Worker Health and Safety
-
- Industrial processes often release harmful particles, fumes, gases, and vapors. Effective industrial ventilation and dust collection systems are essential to protect workers from harmful airborne contaminants, reducing the risk of respiratory illnesses, skin irritation, exposure to hazardous chemicals, or other health issues.
3. Efficient Dust Collection
-
- Performing a full static analysis and sizing the system ductwork, fan, and other equipment to maintain appropriate velocity can prevent issues down the line, such as duct wall degradation and material dropout.
4. Controlling Atmospheric Conditions
-
- By controlling the humidity and removing corrosive chemicals from the air, industrial ventilation systems can prevent equipment degradation, extending the life of machinery and infrastructure.
5. Combustible Dust Hazard Management
-
- In industries where dust, fumes, or vapors are present, improper ventilation can lead to hazardous concentrations that may result in explosions or fires. Adequate measures to address the risks associated with combustible dust/flammable particles, such as explosion prevention systems, are vital in many manufacturing processes.
6. Adaptability for Future Needs
-
- If it is known at the outset that the process could expand in the future, it’s ideal to design excess capacity from the start, instead of trying to overtax an undersized system down the line.
7. Product Quality
-
- Contaminant-Free Environment: In industries such as food processing, electronics, and pharmaceuticals, maintaining a clean environment is crucial for product integrity. Industrial ventilation systems remove dust and other contaminants that can degrade product quality or lead to costly recalls.
- Precision Manufacturing: Contaminants in the air can affect the precision and efficiency of production processes, especially in high-tech and pharmaceutical industries.
In summary, industrial ventilation is essential for manufacturers to ensure safety, regulatory compliance, energy efficiency, and the quality of both the working environment and products.
Professional Services:
- Experienced in small, medium, and large dust collection system design
- Proficient in duct design based on SMACNA (Sheet Metal and Air Conditioning Contractors’ National Association) standards
- Work hand in hand with explosion protection vendors when the dust characteristics require it and have experience with both active and passive explosion mitigation
- Well-versed in hood design that takes into account appropriate capture velocity while keeping system efficiency in mind
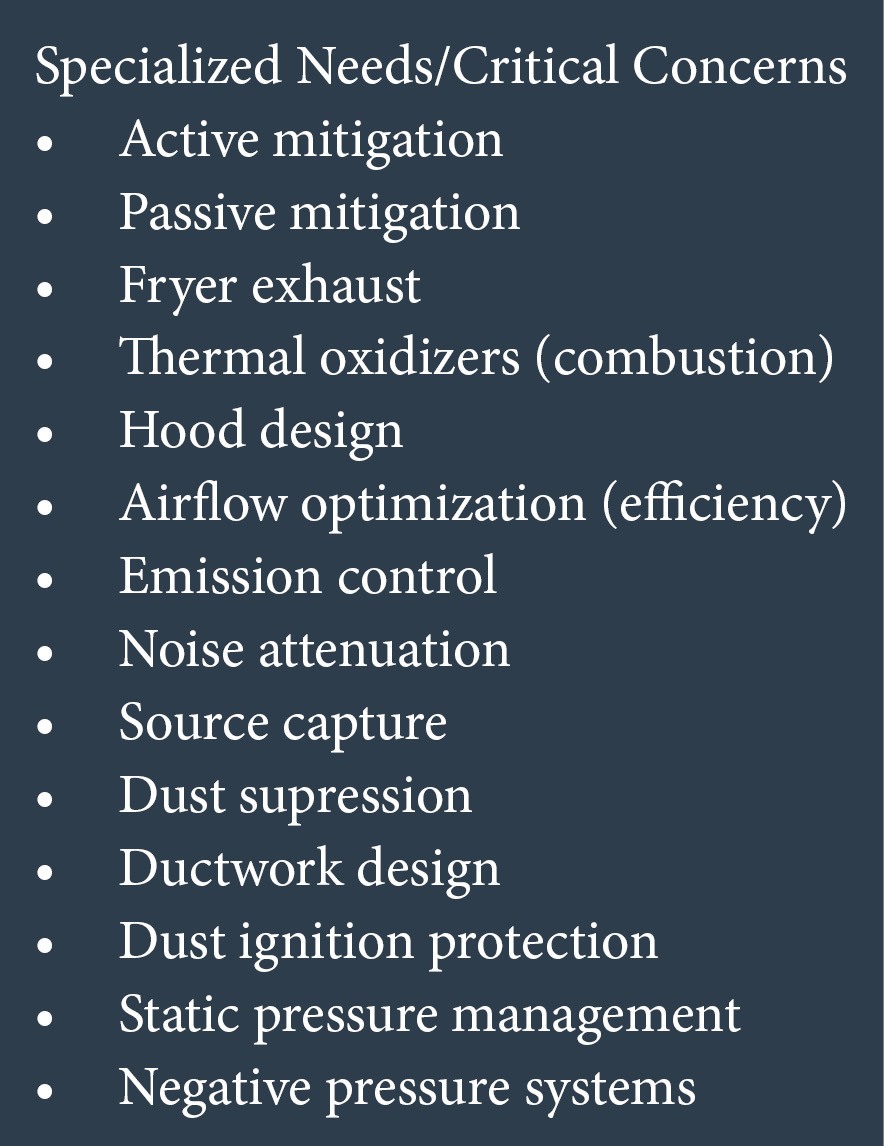
Evidence:
Dust Collection –
- Monsanto – Dust Collection Upgrade
- Marshall, MO
- The JDI Group provided a fully operational dust collection upgrade of the tower, true bulk, and packaging areas at the Monsanto facility in Marshall, Missouri. In addition, our team redesigned the hood in the receiving area to improve dust pickup. We created mechanical and structural drawings for the installation of four diverter valves and two conveyors that were feeding the true bulk and packaging bins.
- JDI obtained soil borings and tests in the area where the new dust collector building is located and the cull bin was relocated. A 3D scan of the existing plant was done to provide background information on the existing plant for the development of a 3D model. During that time, our team also did fieldwork to verify the scan and provide additional details. We used this information to develop process flow and air flow diagrams for the new collectors to validate the collector and fan sizes. The JDI Group created equipment layouts for the new building and for the relocated cull building, as well as for the new diverters and conveyors. From the 3D model, we completed ductwork layouts and hood designs.
- Once everything was worked out in the model, our team developed contractor installation drawings and the bid package. New foundations were designed for the new dust collector building and the relocated cull building. JDI designed support steel for the four new dust collectors, ductwork, and hoods and added the design to the model. From this, drawings were created and added to the construction package. Once the layouts and steel supports were finalized, we created fabrication details to allow ordering of the steel.
- Marshall, MO
- DuPont – Dust Collection Execution
- Hillsdale, MI
- The JDI Group provided detailed engineering and construction drawings for the replacement of an existing dust collection system that had routing issues and additions made to the system without adjustments or rebalancing. Our team provided a new dust collection ductwork system layout, ductwork isometrics for fabrication, mechanical details, and specifications/quotes and structure/foundation for a new explosion isolation valve. We analyzed the existing purlins that support the duct loads and created a roof framing plan, sections, and details for the duct hangers. The new system was installed while the existing one was still in operation to allow for a quick changeover.
- Hillsdale, MI
Fume Collection –
- Confidential Chemical Manufacturer – Plant 1 Ventilation Updates
- Adrian, MI
- The JDI Group provided engineering and design services to fully document the current state of the existing ventilation system in plant 1 of the client’s facility in Adrian, Michigan. The system was originally designed in 2012 by JDI, but since its original installation, the plant has made multiple changes to the system. Our team did fieldwork to record the changes made to the systems, updated project models to reflect the new conditions, and created new drawings to have a complete, updated drawing set.
- Adrian, MI
Ventilation –
- Confidential Chemical Manufacturer – Building 16 Process Ventilation Updates
- Adrian, MI
- The JDI Group provided process mechanical services, including a field visit, to update the building 16 process ventilation system drawings supplied by the client. Our team produced calculated flow rates for each of the drop downs listed on the marked-up drawings, as well as updated the associated detail drawings as the new lines were installed and the pipe specification and information were provided by the client.
- Adrian, MI
- Confidential Chemical Manufacturer – Ventilation Project
- Adrian, MI
- The JDI Group performed a survey and evaluation of the general building ventilation in three PSM-covered process areas: building 7, building 8 (plant 2), and building 16 (plant 1). The evaluation included a review of the existing exhaust fans and a determination of the required number of air changes, make-up air requirements, and a budgetary cost estimate for the installation of the required equipment. JDI provided fieldwork and mechanical engineering and design services necessary to complete the detailed design and equipment specification for the general building ventilation. The system was designed with the intent of preventing the build-up of flammable vapor in the process buildings.
- Adrian, MI
Scrubber Systems –
- Seamless Tubing Manufacturer – Fume and Dust Control
- Youngstown, OH
- The JDI Group, in conjunction with a contractor partner, supported the system upgrade for a new fume and dust control system at an existing pipe-forming process mill.
- The system consisted of a newly designed exhaust hood for the existing pipe forming process, existing dust hoods and pickups, a mist elimination scrubber, three 675 HP exhaust fans, and a 360,000 CFM exhaust stack. Increased dust collection was required on the line due to the nature of the process, which involved blowing a particulate through the formed tube for lubrication.
- JDI performed an extensive field evaluation of the existing conditions, including identifying building constraints that would provide duct routing challenges. Following the performance criteria, JDI created final documentation for equipment and components required to operate in a Pipe Mill environment running 21 operating turns a week for 52 weeks a year.
- We designed the exhaust hood using Autodesk Inventor and routed all ductwork, transitions, and hoods using AutoCAD MEP. This 3D design approach allowed for efficient clash detection amongst all of the disciplines on the project. In addition to providing engineering services and ductwork routing, the stack and all ductwork were fully detailed for fabrication by JDI.
- Youngstown, OH
At The JDI Group, we have extensive experience in fume and dust collection, as well as industrial ventilation systems. We understand that the efficiency and safety of these systems are critical to maintaining optimal air quality and protecting the health of personnel and equipment. By implementing tailored solutions and leveraging our engineering expertise, we ensure that these systems are both effective and reliable, supporting our clients’ operational needs and safety requirements.
Let us know how we can help support your next challenge.