Material handling is a critical aspect of any manufacturing or distribution operation.
Here are three key factors to consider:
- Bigger is not always better: i.e. higher velocity or pressure
- Available power for your system: selecting new systems to work with existing power feeds and panels/designing to their capacity
- Appropriate controls: i.e. standard operating procedures, proper training, equipment safety features, load limitations/weight distribution, continuous monitoring and improvement (PLCs and HMIs), and automation
By carefully considering these factors, manufacturers can design and implement material handling systems that optimize efficiency, safety, and sustainability, ultimately contributing to the overall success of their operations. Guidance from a professional services consultant, such as The JDI Group, will help streamline the process.
Challenges:
- Worker safety
- Efficiency and productivity
- Inventory management
- Space constraints
- Automation and technology integration
- Maintenance and downtime
- Regulatory compliance
- Adaptability and scalability
- Cost management
- Supply chain disruptions
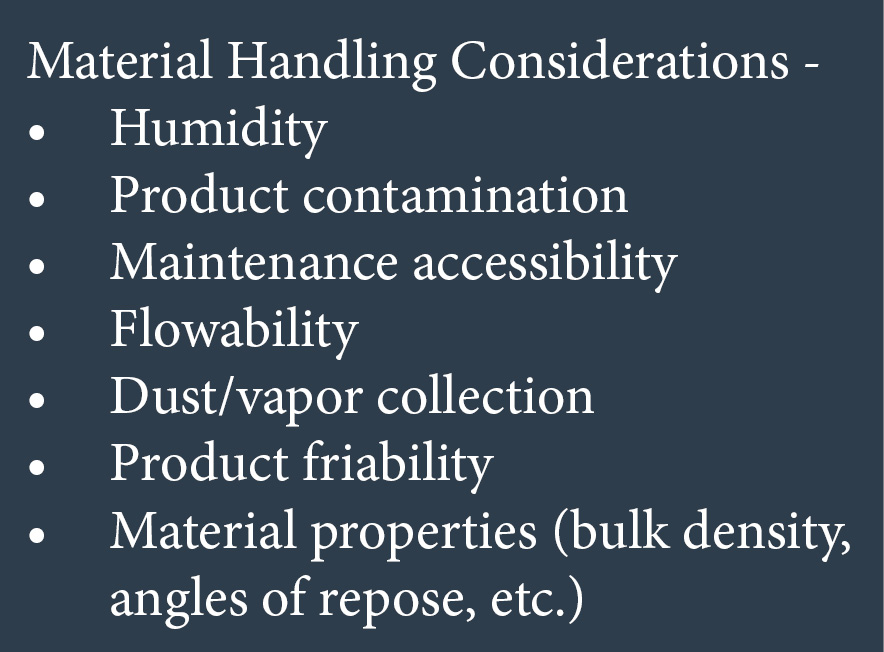

Solutions:
- Worker safety: Provide comprehensive training on safe material handling practices, use ergonomic equipment and tools, and implement safety protocols such as guardrails, signage, light curtains, pull-cords, or E-Stop switches.
- Efficiency and productivity: Implement lean manufacturing principles, such as flowability, to streamline processes, including conveyor systems for continuous material circulation and automation for repetitive tasks.
- Inventory management: Utilize a manufacturing execution system (MES) to help manage your raw materials to finished products. This software is a comprehensive, dynamic system that monitors, tracks, documents, and controls the process of manufacturing goods.
- Space constraints: Maximize vertical space with mezzanine floors or high-density storage systems like vertical carousels and shelving. Optimize layout and workflow to minimize wasted space.
- Automation and technology integration: Gradually introduce automation technologies like Automated Guided Vehicles (AGVs), integrate Supervisory Control and Data Acquisition (SCADA) systems for controlling, monitoring, and analyzing industrial devices and processes, and leverage data analytics for process optimization (PLC and HMI programming).
- Maintenance and downtime: Implement preventive maintenance schedules, conduct regular equipment inspections, use predictive maintenance technologies like condition monitoring sensors, and have spare parts readily available to minimize downtime.
- Regulatory compliance: Stay updated on relevant regulations and standards, conduct regular safety audits, provide ongoing training for employees on compliance requirements, and collaborate with regulatory agencies to ensure adherence (arc flash analysis, mitigation, and training).
- Adaptability and scalability: Design solutions with scalability in mind, ensuring that your infrastructure can accommodate future expansion and changes in demand.
- Cost management: Seek support from professional services consultants to save costs in the long run. Their expertise allows the design of efficient layouts, optimized workflow, and waste reduction, resulting in lower operational costs and higher ROI.
- Supply chain disruptions: Diversify suppliers to reduce dependency on single sources, establish contingency plans for supply chain disruptions, and utilize advanced forecasting tools to anticipate and mitigate potential disruptions.
Working with a consultant that offers a full-service, multi-discipline team with experience in resolving clients’ material handling challenges can provide manufacturers with the expertise, resources, and support they need to optimize their operations and achieve their business objectives.
Professional Services Consultants:
- Bring a wealth of knowledge and expertise in material handling techniques, best practices, and industry standards
- Tailor material handling solutions to meet the specific needs and requirements of your manufacturing operation
- Integrate cutting-edge automation systems and software solutions to streamline your processes
- Are adept at project management and can expedite the implementation of material handling projects
- Help you scale your material handling systems accurately
- Well-versed in regulations and safety standards
- Can free up your internal resources to focus on your core competencies and strategic objectives
Conveyor Design Support
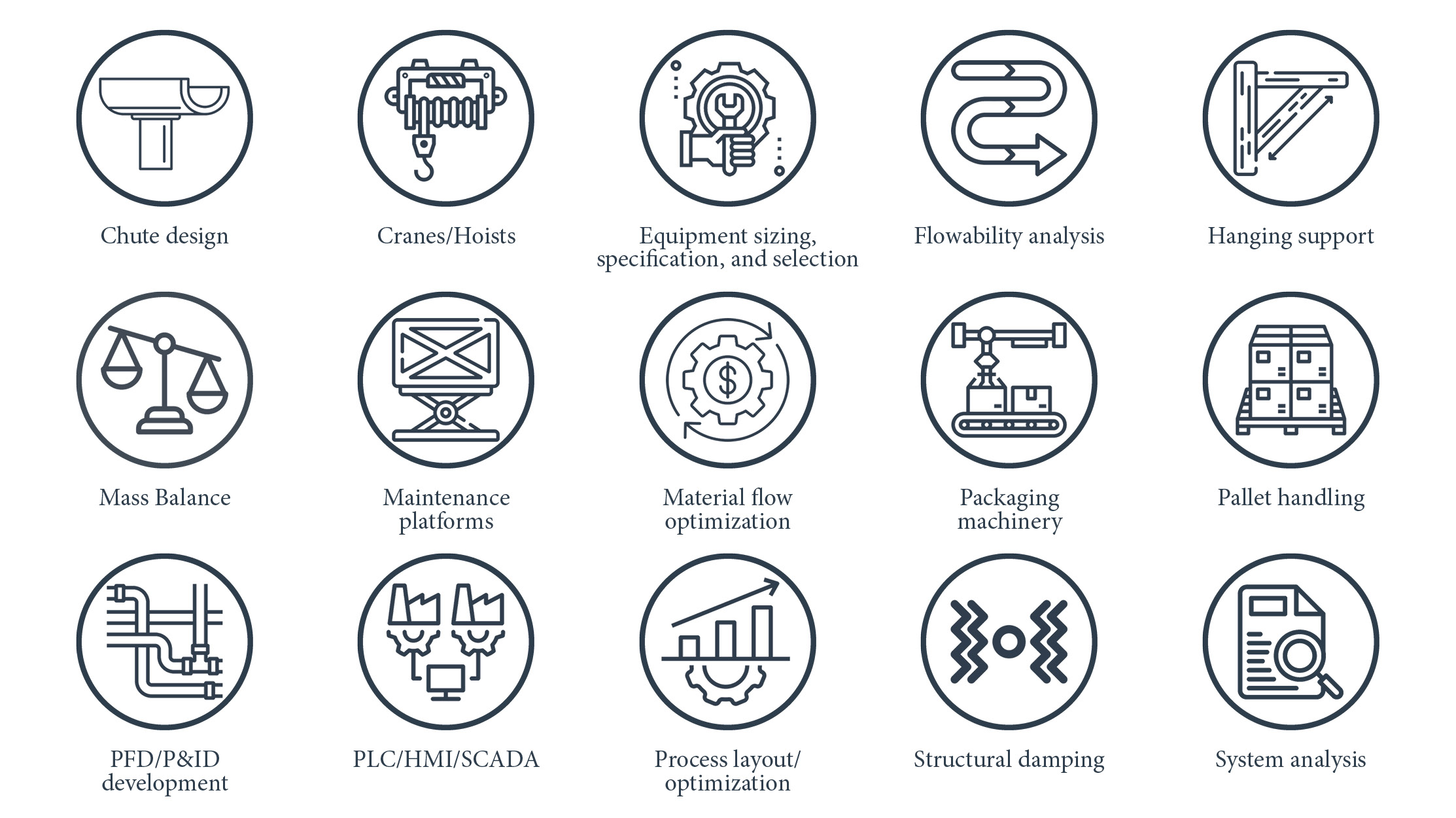
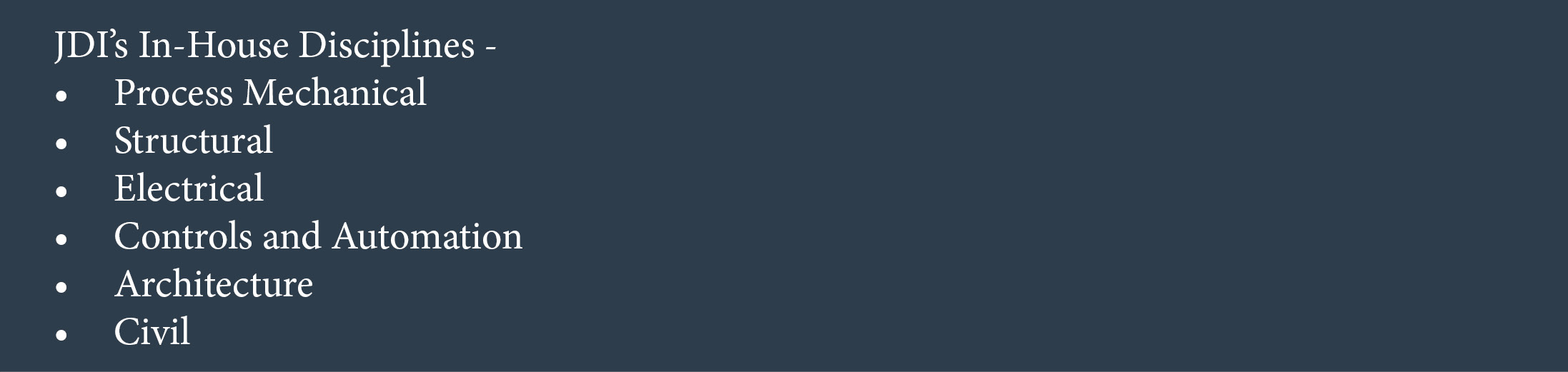
Evidence:
Case Studies –
- Star of the West – Flour conveying system
- Iron Dynamics – Bin bottom/feeder replacement
- OmniSource – Shredding & separation
At The JDI Group, we have extensive experience in all aspects of material handling. We understand that the success of material handling systems hinges on meticulous design and strong structural support. By implementing the right solutions and leveraging our expertise, we ensure that material handling systems operate smoothly and efficiently, supporting our client’s goals and objectives.
Let us know how we can help support your next challenge.